Thanks to a new type of sealing ring design and the use of self-lubricating elastomer materials, the VR ring type SOA is now the preferred choice for applications in the medium pressure range (15-150 bar). In pumps and rotary joints, it was previously almost impossible to use radial shaft seals with elastomer materials safely at high p-v values. High radial forces lead to the seal material seizing into the shaft surface. High loss torques and high friction temperatures are just some of the disadvantages that users have to deal with when using conventional radial shaft seals.
The mechanical and physical overloads at high p-v values are caused by excessive seal gap extrusion between the pressure support and the shaft.
Dynamic sealing effect in the sealing lip area
The operating principle of these springless radial shaft seals is based on the fact that S-shaped diaphragm bodies are fitted over metallic support bodies with a precisely matched preload. The slanted sealing lip adjoining the diaphragm body counteracts the pressure direction of the medium and is supported on the back by the integrated pressure disc. When the diaphragm body is stretched over the metal body, a radial and a tangential force builds up in the diaphragm and sealing lip sections. This radial and tangential force replaces the spring force that is required as a radial force to build up the sealing force in standard seals.
The presence of the tangential force makes it possible to reduce the radial force of this RWDR to a quarter of the radial force of the standard ring. This is the main advantage of this seal design and therefore fulfils the basic requirements that should be placed on every sealing point.
- no run-in marks on the axle even without hardening and grinding
- even on stainless (V2A, V4A) axles
- low power loss, high speeds possible
- high pressure load, high sealing effect
- high service life values
Sealing gap extrusion
Every rotary shaft seal is subject to extrusion when pressure is applied in the sealing lip area in the direction of the side facing away from the pressure, i.e. the sealing material is drawn into the sealing gap between the shaft d1 and the effective diameter DW.
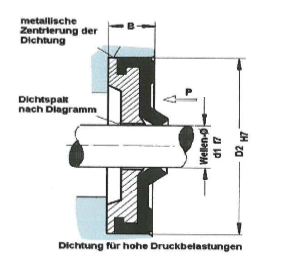
The distance of the sealing gap ds = (DW-dI) / 2 is the determining factor for the p-v value of the sealing point (p-v) = f (ds)
During this process, the elastomeric material in the rear area of the sealing lip between the gap of the pressure support and the shaft moves towards the side facing away from the pressure under the influence of pressure and speed.
The effective diameter Dw is determined either by the the sealing ring design or by the component behind the sealing lip (housing component (housing, disc, etc.) behind the sealing lip.
Under the compressive load p, a much higher radial force Fr and an additional axial force Fa in the direction of the side facing away from the pressure occur due to the sealing material being drawn into the annular gap ds. With rotating shafts, torsion acts on the sealing lip geometry under the influence of the pressure load. This results in high shear stresses in the sealing material. These shear stresses rt are a function f(p, v, µo, ds). It is absolutely necessary to achieve a constant dimension ds over the entire circumference of the sealing gap. In addition, the sealing lip must be supported by a surface set at approx. 30° to the effective diameter Dw so that it does not rest against the shaft with its entire length under pressure.
If the distance ds is too large or uneven, this can lead to material burns and shearing of the sealing lips during operation. The distance ds is therefore the decisive factor as to whether a seal holds under the specified pressure and the specified circumferential speed or is destroyed.
Sealing gap shaft seal SOA
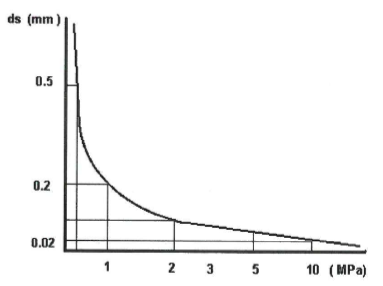
In the VR sealing system, the sealing gap ds is taken into account by the support body bore dimension DW. Higher and dynamically occurring pressure loads require smaller distances ds. Minimum distance values ds were determined for the VR rotary shaft seals under the influence of the pressure load.
In order to be able to absorb high pressures, ds must therefore be small
and the pressure support behind the seal must be made more stable and also more precise. This pressure support has so far been achieved in the standard ring with an additional disc fitted behind the seal
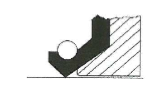
In the VR design SOA, this pressure disc is integrated into the seal structure. The additional metallic centring of the seal in relation to the housing bore makes it possible to achieve extremely low ds values with this design. This ensures that the seal is absolutely centred in relation to the shaft.
This in turn is necessary in order to achieve the same ds dimension over the entire circumference of the sealing gap. Only then can it be guaranteed that the torsion pattern (stress pattern) of the sealing material is constant over the circumference under the influence of pressure and that no material extrusion occurs. Uneven stress ratios in the sealing gap lead to premature failure (tangential cracks) or significantly reduce the service life of the seals.
SOA shaft seal dimensions
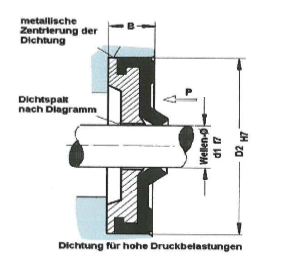
Torque determination
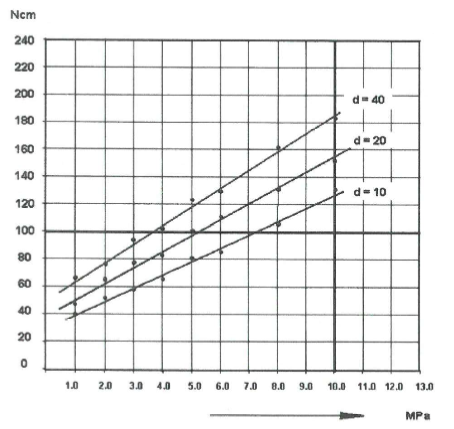
SOA with d3 = -0.03 mm
HNBR 70 Shore
n = 15 rpm
Diagram 2: Torque determination
Torque determination Mt ( torque loss at sealing gap 0.03 mm )
- Under different pressure values and different shaft diameters
- Power loss P = Mt x w
Summary
New type of pressure resistent radial lip seal
New type of pressure resistent radial lip seal for use in the middel pressure range. The reduction of the clearance between shaft and support ring and the amelioration of the elastomer material (slef greasing) led to a complete new design of the radial lip seal. This new type of seal enables the use in the middle pressure range of pumps, especially gasoline pumps.